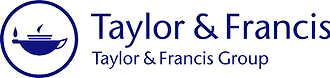

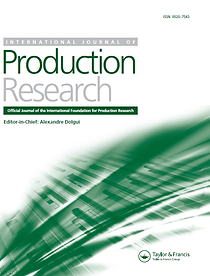
INTERNATIONAL JOURNAL OF PRODUCTION RESEARCH
Additive Manufacturing for Operations and Supply Chain Management
CLICK HERE TO VIEW JOURNAL AND SUBMIT
Guest editors
-
Mirco Peron, NEOMA Business School, France. Emai: mirco.peron@neoma-bs.fr
-
Francesco Lolli, University of Modena and Reggio Emilia, Italy
-
Alain Bernard, Ecole Centrale de Nantes, France
-
Michael Kay, North Carolina State University, USA
-
Manoj Tiwari, IIM Mumbai, India
Submission deadline
31/12/2024
Background
Additive manufacturing (AM) has lately emerged as a disruptive manufacturing technology since it enables a quick and easy production of parts with a level of complexity that is not even conceivably possible using conventional manufacturing (CM) techniques (subtractive technique like casting, rolling, etc.). The aerospace and automotive industries were the forerunners in utilizing the possibilities achievable via producing parts in AM, with huge performance benefits (Westerweel et al. (2018) reported that the production of 25% lighter aileron brackets thanks to AM leads to a fuel savings of 1000 euros per airplane lifecycle), and its use has now spread to other industries and applications. The biomedical industry, for instance, has begun producing implants using AM because it makes it possible to produce implants that match the needs of the human body more closely than CM (Emelogu et al., 2016). Similarly, after-sales companies have been attracted by the opportunity that AM offers to digitalize their inventories since AM makes it possible to reduce stock levels by producing spare parts on demand (Cantini et al., 2022; Sgarbossa et al., 2021). Additionally, AM, allowing to produce parts at the point of use, has an impact on the entire supply chain, not just the production stage. Indeed, by producing parts close to the point of use, the supply chain can become less complex (fewer echelons are needed), have a smaller transportation environmental impact, and be much more responsive (Ivanov et al., 2019; Kunovjanek & Reiner, 2020; Kumar et al., 2016). This is particularly important considering the current times where the global instabilities are affecting our lives and the frequency of natural disasters might increase due to the global warming. In such a context, AM can increase the resilience and viability of supply chains, as well as support humanitarian organizations in the first recovery phase after the occurrence of natural disasters or other disruptive events (Rodriguez-Espindola et al., 2020; Ivanov, 2021; Ivanov et al., 2023; Peron et al., 2022).
Nevertheless, despite all of the potential and advantages of AM listed above, its use is still restricted. Indeed, its diffusion is hampered by a few major limitations. First, the economic benefits indicated above are lessened or even eliminated because AM parts are more expensive than their CM counterparts (Lolli et al., 2022). This is even worse if parts must be qualified in accordance with various standards (ISO, ASTM,...) because only a small number of businesses/institutions are now certified to qualify AM parts (in contrast to CM parts) and current standards are unfavorable to AM (Thomas-Seale et al., 2018), and this has a significant impact on the price of AM parts. Additionally, the still substantial investments required to purchase an AM machine restrict the cases in which manufacturing parts on-site is economically advantageous (Ahmed et al., 2023; Strong et al., 2019). In this perspective new applications of mobile AM hubs are being studied and developed (Cui et al., 2023; https://fieldmade.com/). Moreover, planning and controlling the production of AM parts is a complex task: considering the scheduling of AM production as an example, in fact, decisions on the production scheduling are not straightforward since this is strictly connected to decisions on parts’ orientation (which might be limited due to design requirements) and on parts’ nesting in the building chamber (Zhang et al., 2020; Kucukkoc, 2019). Furthermore, there have been an increasing number of legal actions in recent years for IP infringement when using AM parts (for example, for respiratory valves during the fight against the Covid-19 pandemic (Tareq et al., 2021)). This has a significant negative impact on the opportunities to use AM in the initial recovery phase after the occurrence of natural disasters or other disruptive events. Finally, some dilemmas arise also from an environmental standpoint. By producing parts close to the point of use, AM actually allows to reduce the environmental impact of the transportation phase. However, the AM production process is quite energy-intensive. As a result, considering the entire product lifecycle may not result in a reduction in the overall environmental impact (Top et al., 2023; Demiraly et al., 2023). Thus, it is still unclear when it is truly convenient to adopt AM (Jarrar et al., 2023). This uncertainty further increases if we include in the analysis the risk of disruptions: while on the one hand adopting AM may result in greater costs, on the other hand it may also ensure the viability of the supply chain.
Therefore, this special issue aims at collecting novel and innovative studies that support decision-makers in tackling the above-mentioned dilemmas and issues.
Topics may include (but are not limited to):
-
Adoption of AM in supply chains
-
Digital inventories
-
Impact of AM on supply chain design
-
Impact of AM on supply chain planning and control
-
Hybrid conventional-additive manufacturing supply chain
-
Mobile additive manufacturing
-
AM for supply chain resilience/viability
-
AM for spare parts supply chains
-
AM for biomedical supply chains
-
AM for humanitarian supply chains
-
AM for sustainable supply chains
-
Qualification tests in AM supply chains
-
IP issues in AM supply chains
-
Scheduling and nesting of AM machines
-
Environmental footprint of AM
-
Social sustainability of AM
Both theoretical and applied research contributions and real-world application feedback are welcome.
References
Ahmed, R., Heese, H. S., & Kay, M. (2023). Designing a manufacturing network with additive manufacturing using stochastic optimization. International Journal of Production Research, 61:7, 2267-2287.
Cantini, A., Peron, M., De Carlo, F., & Sgarbossa, F. (2022). A decision support system for configuring spare parts supply chains considering different manufacturing technologies. International Journal of Production Research, 1-21.
Cui, W., Yang, Y., & Di, L. (2023). Modeling and optimization for static-dynamic routing of a vehicle with additive manufacturing equipment. International Journal of Production Economics, 257, 108756.
Demiralay, E., Razavi, N., Kucukkoc, I., Peron, M. (2023). An Environmental Decision Support System for Determining On-site or Off-site Additive Manufacturing of Spare Parts. IFIP International Conference on Advances in Production Management Systems, 563-574.
Emelogu, A., Marufuzzaman, M., Thompson, S. M., Shamsaei, N., Bian, L. (2016). Additive manufacturing of biomedical implants: A feasibility assessment via supply-chain cost analysis. Additive Manufacturing, 11, pp. 97–113.
Ivanov, D. (2021). Supply Chain Viability and the COVID-19 pandemic: a conceptual and formal generalisation of four major adaptation strategies, International Journal of Production Research, 59:12, 3535-3552
Ivanov, D., Dolgui, A., & Sokolov, B. (2019). The impact of digital technology and Industry 4.0 on the ripple effect and supply chain risk analytics. International Journal of Production Research, 57:3, 829-846.
Ivanov, D., Dolgui, A., Blackhurst, J. V., & Choi, T.-M. (2023). Toward supply chain viability theory: from lessons learned through COVID-19 pandemic to viable ecosystems. International Journal of Production Research, 61:8, 2402-2415
Jarrar, Q., Belkadi, F., Blanc,R., Kestaneci, K., & Bernard, A. (2023). Knowledge reuse for decision aid in additive manufacturing: application on cost quotation support. International Journal of Production Research, 61:20, 7027-7047.
Kucukkoc, I. (2019). MILP models to minimise makespan in additive manufacturing machine scheduling problems, Computers & Operations Research, 105, 58-67.
Kumar, M., Graham, G., Hennelly, P., & Srai, J. (2016). How will smart city production systems transform supply chain design: a product-level investigation, International Journal of Production Research, 54:23, 7181-7192
Kunovjanek, M. & Reiner, G. (2020). How will the diffusion of additive manufacturing impact the raw material supply chain process? International Journal of Production Research, 58:5, 1540-1554.
Lolli, F., Coruzzolo, A. M., Peron, M., & Sgarbossa, F. (2022). Age-based preventive maintenance with multiple printing options. International Journal of Production Economics, 243, 108339.
Peron, M., Sgarbossa, F., Ivanov, D., & Dolgui, A. (2022). Impact of Additive Manufacturing on Supply Chain Resilience During COVID-19 Pandemic. Supply Network Dynamics and Control (pp. 121-146). Cham: Springer International Publishing.
Rodríguez-Espíndola, O., Chowdhury, S., Beltagui, A., & Albores, P. (2020). The potential of emergent disruptive technologies for humanitarian supply chains: the integration of blockchain, Artificial Intelligence and 3D printing. International Journal of Production Research, 58:15, 4610-4630.
Sgarbossa, F., Peron, M., Lolli, F., & Balugani, E. (2021). Conventional or additive manufacturing for spare parts management: An extensive comparison for Poisson demand. International Journal of Production Economics, 233, 107993.
Strong, D., Kay, M., Conner, B., Wakefield, T., & Manogharan, G. (2019). Hybrid manufacturing—Locating AM hubs using a two-stage facility location approach. Additive Manufacturing, 25, 469-476.
Tareq, M. S., Rahman, T., Hossain, M., & Dorrington, P. (2021). Additive manufacturing and the COVID-19 challenges: An in-depth study. Journal of Manufacturing Systems, 60, 787-798.
Thomas-Seale, L.E.J., Kirkman-Brown, J.C., Attallah, M.M., Espino, D.M., & Shepherd, D.E.T. (2018). The barriers to the progression of additive manufacture: Perspectives from UK industry. International Journal of Production Economics, 198, pp. 104–118.
Top, N., Sahin, I., Mangla, S. K., Sezer, M. D., & Kazancoglu, Y. (2023). Towards sustainable production for transition to additive manufacturing: a case study in the manufacturing industry. International Journal of Production Research, 61:13, 4450-4471
Westerweel, B., Basten, R. J., & van Houtum, G. J. (2018). Traditional or additive manufacturing? Assessing component design options through lifecycle cost analysis. European Journal of Operational Research, 270(2), 570-585.
Zhang, J., Yao, X., & Li, Y. (2020). Improved evolutionary algorithm for parallel batch processing machine scheduling in additive manufacturing. International Journal of Production Research, 58:8, 2263-2282.